Jorgensen Steel Enhances Cutting Capabilities with AKS accu-kut Plasma Technology
In a relentless pursuit of precision and efficiency, Jorgensen Steel, a U.S.-based steel fabrication company, found itself facing a daunting challenge with their laser cutting systems. The quality of the laser-cut components was lacking, especially on materials exceeding ¼-inch thickness. Overall, laser technology was falling short of expectations, posing a significant hindrance to their operational excellence. Jorgensen Steel realized it needed a transformative solution to uphold its commitment to delivering top-notch products. The answer to their challenge materialized in the form of AKS Cutting Systems’ state-of-the-art plasma cutting technology.
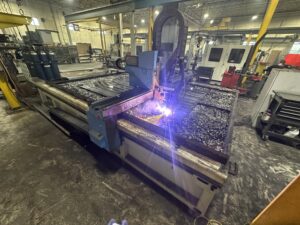
AKS accu-kut in action inside the Jorgensen Steel facility
Plasma Delivers Better Results at a Lower Price
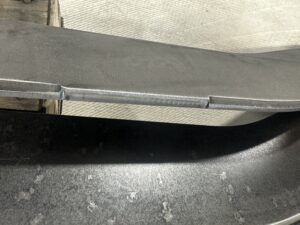
A compound bevel cut combining Top Y bevel and straight cut on the same geometry
Jorgensen Steel implemented AKS’ accu-kut — a top-of-the-line plasma cutting technology. Not only did it address their concerns regarding the quality of cuts, it did so at a lower price point. The superior quality of the components, combined with a substantially reduced cost per cut, heralded a new era of manufacturing excellence for the company. Daryl Blashfield, Operations Manager at Jorgensen Steel, noted, “wow, these aren’t even close to our other supplier.”
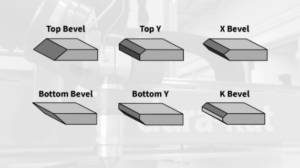
Types of bevel cuts reliably cut by the AKS robo-kut
Overall, the speed and reliability of the AKS accu-kut allowed Jorgensen Steel to operate with increased efficiency, resulting in reduced production costs.
Not only was the company able to lower overall costs, it also gained the ability to bevel parts. Beveling parts was previously impossible with Jorgensen Steel’s laser cutting machine. However, it’s a simple process with AKS’ equipment. The AKS accu-kut features a robo-kut five-axis beveling system, allowing for a wide range of bevel cuts. That, combined with Hypertherm XPR definition plasma power supplies, allowed for enhanced quality in their parts.
Jorgensen Steel Triples-Down on Plasma Cutting
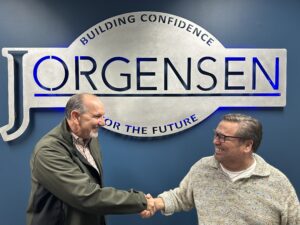
Kent Phillip, VP of Operations at AKS Cutting Systems [left] visits Matt Jorgensen, President of Jorgensen Steel
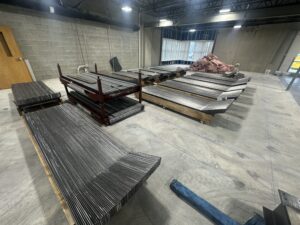
Jorgensen Steel cut 36,000 of the above ¼” mild steel parts using the AKS accu-kut. These included complex beveling on multiple sides.
Jorgensen Steel’s successful transition from laser to plasma cutting technology underscores the importance of making well-informed decisions when it comes to manufacturing processes. By embracing the versatility and efficiency of plasma cutting, Jorgensen Steel now stands as a prime example of a company that not only meets their customers’ demands, but exceeds them. In the end, this change allows them to uphold their commitment to delivering cost-effective, quality products.
About AKS Cutting Systems
AKS Cutting Systems is a leading provider of CNC plasma and waterjet cutting machines. As a fourth-generation, family-owned and operated company, AKS has a strong reputation for durability, accuracy, and reliability with thousands of installations worldwide. For sales inquiries, please contact info@AKSCuttingSystems.com.
About Jorgensen Steel
Jorgensen Steel is a U.S.-based steel fabrication company, located in Tekonsha, Michigan. Started in 2001, the company services a wide range of industries, including the emergency response, oil and gas, and aerospace sectors, among others.
Download This Asset
Looking to download this asset to save for later? Click here.