When a business relies on plasma cutting machines to keep production rolling, preventive maintenance is a requirement of a successful operation.
Without it, even the highest quality machine will show signs of premature wear, experience inferior cut quality and eventually suffer from costly downtime. To keep your AKS Cutting Systems machines running optimally, we’ve broken down key maintenance tasks based on the frequency with which they should be performed. Use this as a general guide to keep these complex machines in top working order.
Daily Maintenance Tasks
- Wipe the bearing rails with either a dry rag or one with a small amount of WD-40 on it. The goal is to remove dust and debris from the bearing rails, as well as any grease that the bearings themselves have left on the bearing rails. This task will significantly increase the life of these components.
Weekly Maintenance Tasks
- Use a compressed air line to blow out dust from the plasma itself, as well as the radiator and control cabinet. In addition to increasing the life of these components, removing dust build-up will help prevent machine malfunctions.
Monthly Maintenance Tasks
- Grease all the bearings and check their coolant level. Remember, less is more: add a small amount of coolant and a minor shot of grease, so as not to overload the bearings.
- Check to make sure the bridge is square by performing a tension test. Home the axes and drive the bridge to the middle of the table, check the rail and dual gantry position values, press the e-stop, then watch the values for a large numerical change. Find a complete bridge squaring guide here.
- Check for software updates. For XPR plasma cutting systems, updates can be found on Hypertherm’s website. Check there for firmware or Phoenix updates, or contact AKS to learn more.
Long-Term Maintenance Tasks
- Replace torch leads and gas leads at certain intervals, depending on machine type. For example, an HPR’s leads have a shorter lifespan than those of an XPR, so they will need to be changed more often, usually about once every five years.
Long-Term Maintenance Tasks
As a rule of thumb, it’s time to replace consumables when there is a visual difference in cut quality. As an example, when cutting full sheets, look at the first part cut and the last part cut to compare the quality of the edges. If there’s a noticeable difference between the two, replacement is needed. It’s important to remember to always clean the machine after changing consumables.
- While an electrode is made mostly of copper, the center is hafnium — this is where the arc of the plasma originates. During use, that hafnium very slowly deteriorates and burns away. The actual values for consumables being worn out is the depth of the hafnium that is in the center of the electrode. Using an electrode depth gauge to measure the divot in the hafnium center, a value of .040” or more is the threshold for replacement.
- When changing the electrode, always change the nozzle along with it. This is more efficient in the long run, minimizing the amount of time spent replacing components. Changing each separately reduces the overall life of the new consumable and the torch is taken apart more often than necessary.
- Replacing the shield part, the copper cone, is a five-to-one ratio, meaning the electrode and nozzle will require changing roughly five times before the robust shield needs to be replaced. The only time the shield requires changing is if its center hole starts to malform and is no longer a perfectly round circle.
- If the above consumables have been changed and the machine still has poor cut quality, change the inner and outer retaining caps. There’s no clear way to tell if the retaining cap is bad, other than poor cut quality after all other consumables have been changed.
Contact AKS to learn more about machine features, preventive maintenance and more.
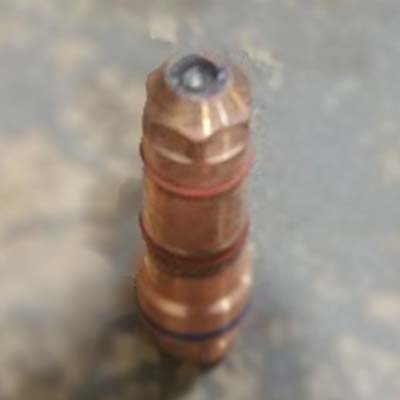
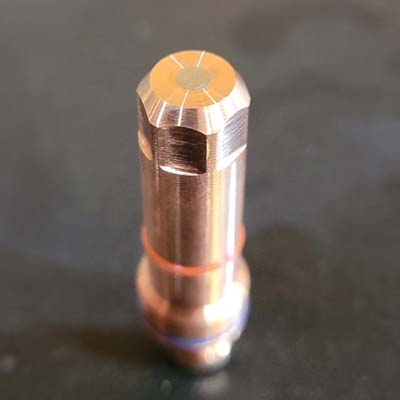